平均速度和平均速率的区别_平均速度怎么计算
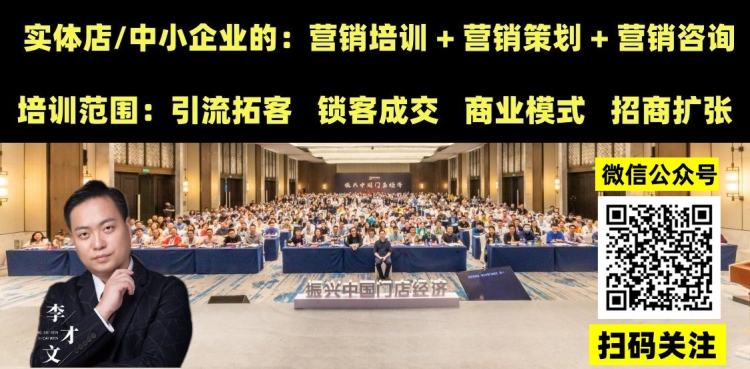
旧时的工艺循环...
在精工工艺中,时间对于每一项工序都是不可或缺的元素。每位参与生产的员工对此术语都不陌生。但仍旧有些许误解围绕它的具体定义。其实,周期时间,简单而言,是制造一个零件所需的最快且可重复的时间段。
时间就是金钱。
我在网上看到的许多关于循环时间的定义都较为宽泛,往往描述为完成某一过程所需的总时间。就实际操作而言,这一描述显得过于笼统。我认为更具体的定义是:
周期时间特指生产一个零件时,排除故障、缺陷和其他延迟等损失的最快可重复时间。
与大多数时间度量一样,周期时间同样存在两种形态:实际周期时间和目标周期时间。实际周期时间即当前的生产周期,而目标周期时间则是我们期望达到的理想状态。
在理解与运用中仍存在一些模糊地带。比如,在批量生产中,周期时间是指整个批次的完成时间,还是单个零件的加工时间?依据不同需求,两种理解均有其合理性。然而遗憾的是,尚未有一个被广泛接受的专业术语来区分它们。
在此需要强调的是,上述定义并非普遍认同的规范。确实有部分从业者将周期时间理解为包含损失在内的总时间。这种做法容易引发混淆。
我强烈建议在计算周期时间时不包括任何计划外的损失或延迟。
当与他人讨论周期时间时,务必明确双方所指的具体含义。在LinkedIn上的TPS原则和实践讨论中,更倾向于将周期时间定义为不包含任何损失的时间段。感谢所有为此讨论做出贡献的同仁。
计算周期时间的常见误区在于简单地将工作时间除以生产零件数量。这种方法看似简单,实则包含了所有生产过程中的损失和故障。即使是在最顺利的情况下,这种方法仍无法准确反映真实的生产速度。
确定周期时间的另一种常用方法是在数据表中查找。机器在制造之初会预设相应的时间,同样地,对于手工操作也有关于速度的可用数据。这些数据往往并不完全准确。
比如在一台注塑机中,“官方”的周期时间可能仅包括注射和冷却环节的时间,而不涵盖模具的开合和取放等过程。所提供的数值往往并不完全代表实际的可重复周期时间。
对于人工操作而言,虽然有基于MTM或REFA数据的可用时间作为参考,但这些数据通常包含了如上厕所或其他休息时间的额外百分比(约5%至25%)。虽然我们可以将这些因素纳入对操作员平均速度的计算中,但在考虑生产峰值速度时却不能将其计入。
为了获取准确的循环时间,最好的方法是在生产过程中多次测量实际操作的单个零件完成所需的时间。通过对多次测量结果的比较分析来找出最可重复的周期时间。
在测量过程中需要注意异常值的影响。最小值并不总是代表可重复的周期时间。算术平均值也容易受到极端值的影响而扭曲结果。在处理数据时需要谨慎选择合适的统计方法。
除了算术平均值外,中位数和百分位数也是常用的数据表示方法。中位数可以帮助我们了解数据的大致分布情况,而百分位数则可以提供更详细的分布信息。
在确定合适的周期时间时,应综合考虑数据的整体分布情况以及实际生产过程中的可重复性。绘制数据图表并仔细分析可以帮助我们更准确地找出可重复的周期时间。
虽然存在多种测量周期时间的方法,但每一种方法都有其优缺点。无论采用哪种方法,都需要在实际操作中进行验证和调整以确保结果的准确性。
尽管我在接下来的文章中(如何测量周期时间的第二部分)将进一步探讨过程步骤顺序的变化、不同零件类型带来的不同周期时间以及关于提高周期时间准确性的通用建议等话题,但无论如何我们都应牢记:准确测量并理解周期时间是实现高效生产的关键。
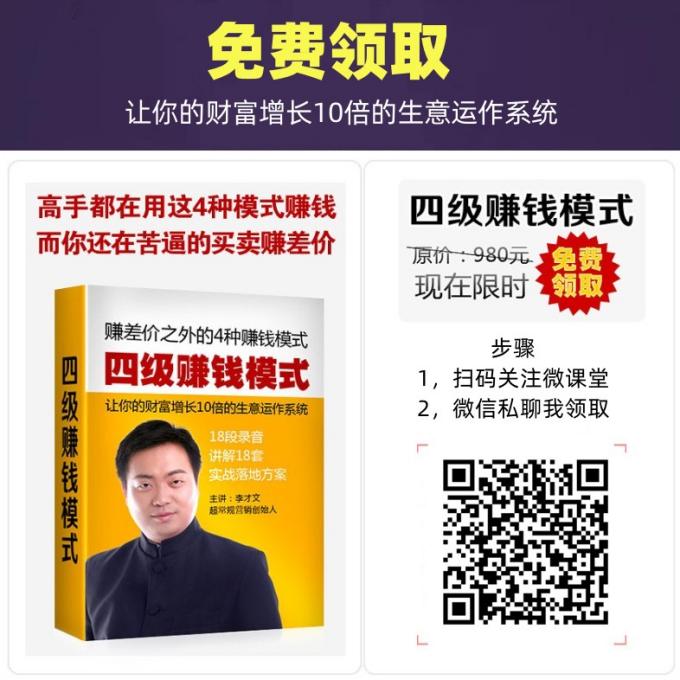