车间的工作内容
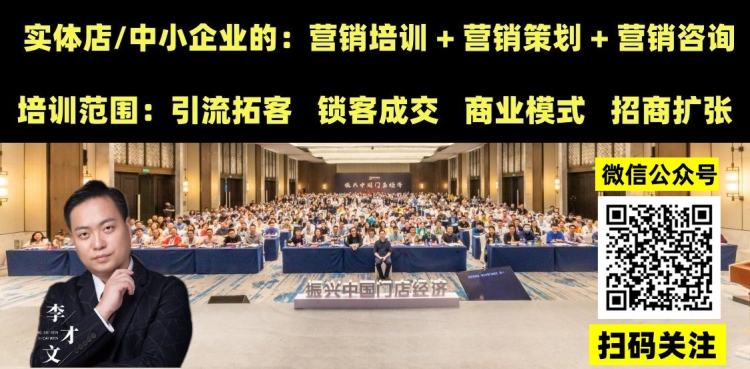
执行标准:
- 车间环境需使用5S检查表(包含32项检查要点)进行定期扫描。
- 度需按照ISO 14644标准进行监测,电子车间需保持25±2℃/RH50±5%的适宜环境。
工具支持:
- 采用华为工业平板配合定制检查APP进行数字巡检终端。
- 引入智能环境监测系统,一旦数据超标即刻自动报警。
案例实证:
某汽车零部件制造厂实施标准化班前检查后,设备启动异常率显著下降45%,此数据来源于2023年JIPM的统计。
具体执行措施:
- 物料管理:利用Zebra DS2208扫码枪,对首件物料与BOM进行扫码核对,确保一致性。
- 设备预检:实施OEE预检制度,确保设备联网率超过95%,并采用OPC UA协议进行数据交互。
- 工艺校验:通过MES系统自动比对电子SOP版本,保证工艺执行的准确性。
- 人员配置:设置技能矩阵看板,多能工覆盖率需达到80%或以上。
典型问题及应对:
某电子厂因疏忽锡膏回温时间,导致出现批次性虚焊问题。为此,需强化人员状态确认及目标传达的环节,确保生产流程的每个环节均无疏漏。
每日工作细化:
- 人员状态与目标传达(07:50-07:55):采用旷视人脸识别考勤系统,确保人员准确到岗,同时实时更新KPI看板,反映小时产能、直通率及报废率等关键指标。对于新投产的重点机型,系统将进行红色提示预警。
- 昨日复盘与今日指令(07:55-08:00):进行OEE分析和TOP3问题,使用A3报告格式记录并跟进。通过车间广播系统同步生产指令至全产线,关键岗位需进行二次确认,并由班组长签字确认。
行业标杆比较:
博世苏州工厂通过优化班前会效率提升40%,其采用Andon系统实时采集作业周期时间,一旦偏差超过5%即刻报警。还应用Kineo CAMS系统检测标准作业的符合率。
其他行业最佳实践案例:
丰田广州工厂通过实时监控,动作浪费减少32%,其应用U型生产线平衡率公式进行计算,并设定目标平衡率,每小时更新电子平衡墙数据。某家电企业则通过ECRS法优化产线,平衡率从68%提升至87%,并建立四级响应体系和不良品追溯的区块链技术。
数据驱动的改善:
美的集团通过快速响应机制,停线时间显著下降55%。其采用水蜘蛛配送+AGV协同系统,确保配送准时率超过98%,并建立双箱制物料预警系统,当余量低于2小时即自动补货。利用AI视觉识别系统和安全积分看板提升生产安全水平。
决策支持与预排产:
通过APS系统进行预排产,确保工单齐套率超过95%。模具预加热系统则自动启动并维持目标温度的±3℃精度。应用BI系统生成决策影响分析报告,并建立决策案例库以应对300+典型场景。
企业成果与核心价值:
多家标杆企业如上汽通用、和海尔均通过各自的改进措施实现生产效率与管理水平的提升。核心价值在于构建"计划-执行-检查-改进"的制造现场闭环,实现从经验管理到数据驱动的转变,并落实"三现"(现场/现物/现实)的管理原则。
持续改进建议:
- 定期开展"Gemba Walk"现场行走活动并使用定制检查清单。
- 建立生产主管数字化驾驶舱以整合MES/ERP/SCADA等数据。
- 实施"三星认证"体系对生产主管进行能力评价与提升。
“生产主管的战场永远在车间地面,不在办公室”——这一丰田生产系统的箴言时刻提醒着每一位生产管理者,实地执行与持续改善是生产管理的核心。
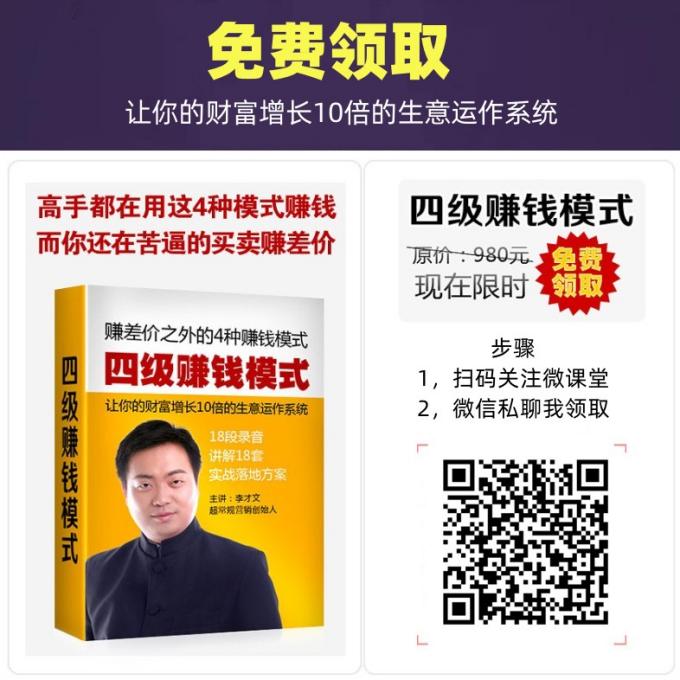