工控系统包括哪些系统
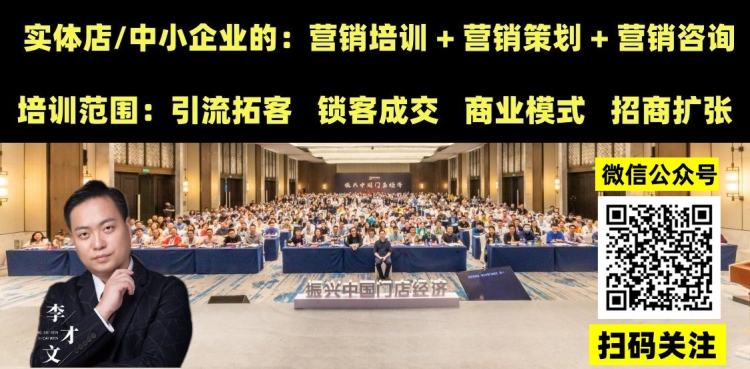
随着工业技术的迅猛进步,集散控制系统和现场控制系统相继诞生,它们共同构成了现代工业过程控制的核心。在这其中,PLC(可编程逻辑控制器)、DCS(分布式控制系统)以及FCS(现场总线控制系统)是三大核心控制系统。关于这三者的起源,有人认为是FCS由PLC发展而来,也有人认为是DCS的延伸。尽管存在不同的观点,但它们之间确实存在着密不可分的联系,同时各自具有独特的优势。
PLC控制器是一种专为工业环境设计的数字运算操作系统。它采用可编程的存储器,用于存储程序、执行逻辑运算、顺序控制、定时、计数与算术操作等。通过数字式或模拟式输入或输出,PLC能够控制各种类型的机械或生产过程。
DCS,即计算机分布式控制系统,是20世纪70年代中期随着技术的发展而兴起的。它结合了控制技术、计算机技术、图像显示技术以及通信技术,实现了对生产过程的、控制和管理。DCS打破了传统控制仪表的功能局限性,并解决了早期计算机系统过于集中带来的风险。
FCS的核心是总线协议,基础是数字智能现场设备,本质是信息处理现场化。它以数字信号为主导,连接所有设备,提供全数字化信号。这种系统的出现,使得控制功能更加分散,适用于各种复杂环境。
对于大型PLC构成的过程控制系统,其主要特点包括结构从上到下的层次性、PID控制功能的实现、网络构成的多台PLC协同工作以及主要用于工控中的顺序控制等。而DCS系统则是树状结构,其中通信是关键。PID控制器连接计算机与现场仪器仪表,信号系统包括开关量信号和模拟信号。FCS系统的基本特点则体现在其3C技术的融合、现场设备的高度智能化以及双向数字通信总线的使用等。
在对比DCS与PLC系统时,可以发现DCS是一种分散式控制系统,可实现任何装置的功能与协调,而PLC只是一种控制装置。DCS系统网络实时可靠,支持大量扩展接口;而PLC系统在通信和网络安全性方面相对较弱。在硬件可靠性方面,DCS和PLC相差无几。但在软件方面,PLC具有优势,特别是在高速顺序控制中。DCS实现顺序联锁功能相对较弱,逻辑执行速度也不如PLC。而FCS系统则兼具DCS和PLC的特点,并且实现了性的跨越。它具备全开放性、全数字化、彻底分散的特点,可以提供更多的信息量,并实现对现场设备的远程诊断和维护。
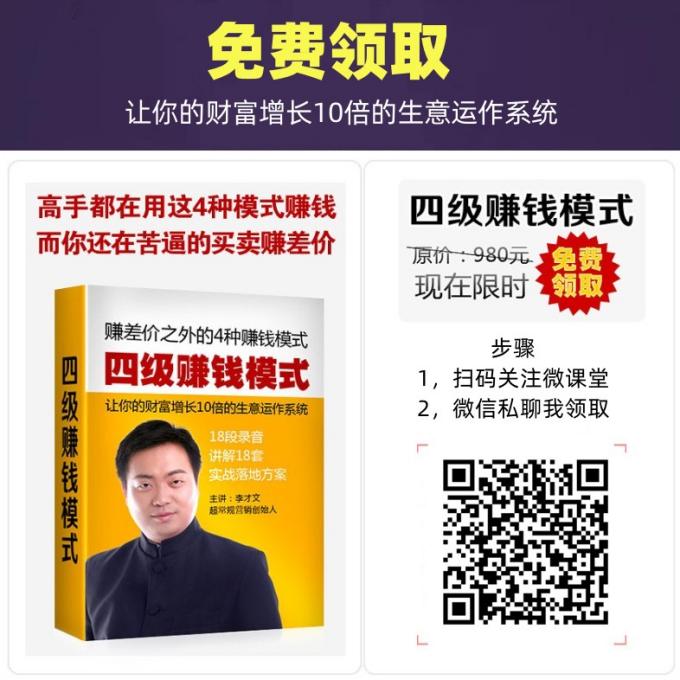