APQP包装评估流程揭秘:关键阶段与实施要点全解析
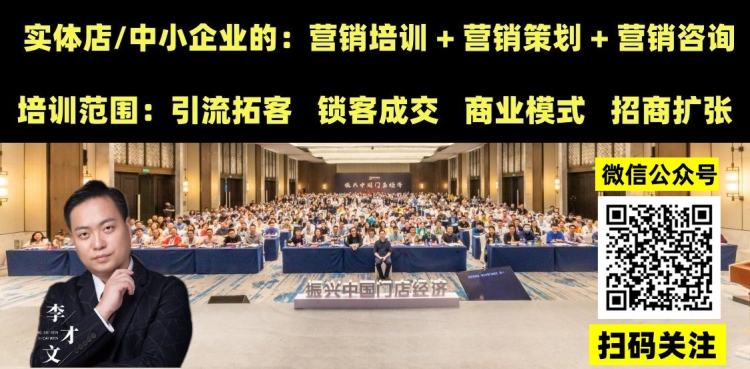
我们继续深入探讨APQP(先进产品质量规划)的第二阶段——产品设计与开发验证阶段:
2.1 DFMEA(后续详细讲解)
★ DFMEA是一种评估失效可能性及其后果的分析技术,它帮助团队在产品设计的初期就预见到潜在的问题。
★此分析是动态文件,随着顾客需求和期望的变化,文件会不断更新。
★由于产品和过程特性的复杂性,DFMEA可能需要进行多次分析。
★要特别注意不陷入表面现象的误区,需深入分析根本原因。
★通过DFMEA,小组有机会评审之前的选择并做出必要的更改。
2.2 可制造性和装配性设计
★这是一种同步工程过程,旨在优化设计功能、可制造性和易于装配性之间的关系。其目的是确保设计不仅在理论上可行,而且在实践中也是可实施的。
★活动的程度取决于确定的顾客需求和期望的范围。
★需要考虑的方面包括:设计、概念、功能和对制造变差的敏感性、制造和/或装配过程、尺寸公差、性能要求、部件数、过程调整以及材料搬运等。
2.3 设计验证
设计验证的目标是确保产品设计满足第一阶段中描述的各项活动中的顾客要求。
2.4 设计评审
★设计评审是由设计工程部门领导,并包括其他受影响部门的定期安排会议。它不仅是防止问题和误解的有效方法,还提供了进展和向管理者报告的机制。
★设计评审技术检验只是其中一部分,更是一系列的验证活动。评价方面应包括设计/功能要求的考虑、正式的可靠性和置信度目标、部件/子系统/系统工作循环等。
★设计评审的主要功能是设计验证进展。
2.5 样件制造——控制计划
样件控制计划描述了样件制造过程中的尺寸测量和材料与功能试验。产品质量策划小组应确保制定样件控制计划。
2.6 工程图样(包括数学数据)
★工程图样必须包括特殊(如法规和安全性)特性,这些特性必须在控制计划上明确指出。
★应对工程图样进行评审,以确保每个零件的尺寸布置都有足够的数据支持。应清晰标识控制或基准平面/定位面,以便为现行的控制设计适当的功能量具和设备。
以下为部分后续内容的大纲形式,详细内容待续:
2.7 工程规范
对控制规范的详细评审将有助于识别有关部件或总成的功能、耐久性和外观要求。
样本容量、频率和接受标准一般在工程规范的过程试验一章中确定。
否则,样本容量和频率由决定并列入控制计划中。
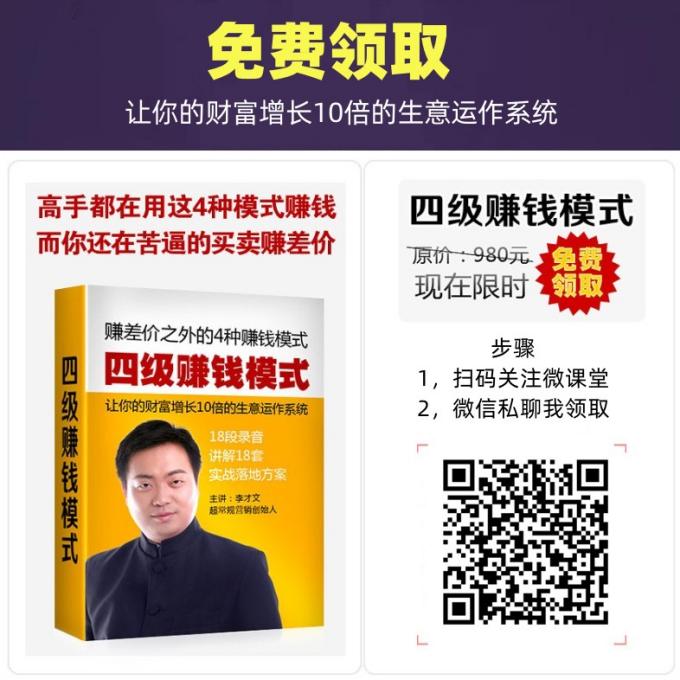