车间一天工作安排
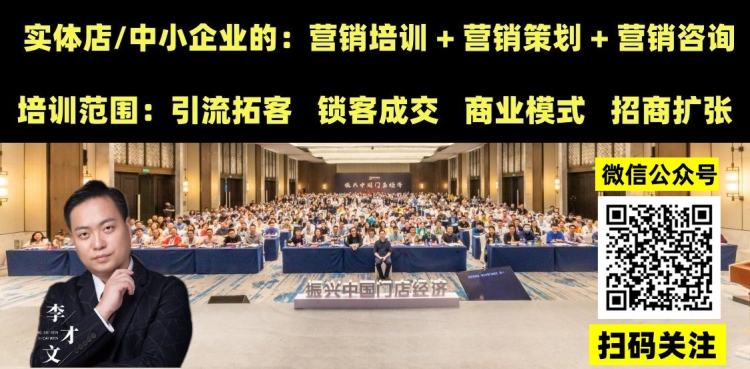
本文将探讨制造车间中车间需密切关注的四个重要监控领域:计划、物料、工艺和状态。结合实际操作经验和数字化管理工具,目标在于提升生产效率、确保产品质量、降低生产成本,实现管理的精细化和数字化。
生产计划是车间的“作战蓝图”,缺乏计划会导致效率损失超过一定百分比(根据行业研究数据)。
一、智能排产系统详解
1. 工具利用:高级计划排程系统(APS)能够动态优化生产顺序。
2. 实际案例:某家电子制造企业导入APS后,计划的实现率从78%跃升至92%。
二、订单的优先级管理
1. ABC分类法应用:
A类(关键客户订单):需保证100%准时交付。
B类(常规订单):允许在正负8小时内有所调整。
C类(内部临时订单):可适度延迟至多24小时。
三、动态调度机制详解
1. 异常响应策略:当计划延迟时,需判断瓶颈工序,并采取备用设备或增派人员等紧急措施,然后评估产能缺口,并协调外部资源进行支援。
2. 数据看板实时监控:计划达成率每小更新,偏差超过5%的项将自动高亮显示。
四、物料管理与齐套率提升
1. 齐套率计算公式:齐套率等于齐套工单数除以计划工单数再乘以100%。控制标准要求当日生产工单齐套率需达到98%以上。
2. 安全库存策略执行:通过动态安全库存模型(SS)确保合理库存水平。
3. 供应商协同机制:采用VMI(供应商管理库存)模式,关键物料由供应商现场驻仓管理,并实施JIT(准时制)到货策略,确保物料配送时间精确到正负15分钟内。
4. 数字化预警工具应用:通过RFID物料追踪技术实时显示物料位置和数量,同时Andon系统在缺料时能自动触发声光报警。
工艺参数的微小偏差可能导致产品不良率显著上升(根据汽车行业研究数据)。
五、工艺参数监控与标准化作业推进
1. SPC(统计过程控制)的使用:关键参数的CPK值需大于等于1.33。同时引入防错装置,如扭矩枪未达标会自动锁止,温度超限则会停机。
2. SOP(标准化作业)的实施与管控:强调SOP符合率计算及执行标准,确保电子组装行业内的执行率至少达到95%。
3. 质量追溯系统的建立:MES系统记录操作工号、设备参数和物料批次信息,同时采用激光打标技术实现产品全程可追溯。
4. 员工技能矩阵的构建:明确不同技能等级的认证标准和权限范围。
六、人效与班组活力提升策略
1. 评估班组活力指数的多个维度及计算公式:包括出勤率、技能匹配度和异常响应速度等。
2. 人机工程优化措施:设定工位设计标准,如物料拿取高度需在0.75-1.25米之间,以符合工学要求,同时确保同一工序内的步行距离不超过3米。
3. 状态监测工具的利用:如智能手环可实时监测心率和动作频率,并在员工疲劳时自动提醒;视频AI分析则能识别员工分心行为。
4. 班组激励机制的构建:包括效率奖金阶梯算法等,以激励员工提升工作效率。
车间的四大核心是系统思维与数据驱动的结合。通过将计划、物料、工艺和状态转化为可量化指标,并借助数字化工具进行实时监控,方能实现效率、质量、成本的平衡。请记住:在车间管理中没有“差不多”这一说,只有精确到分钟、管控到微米的严格标准!
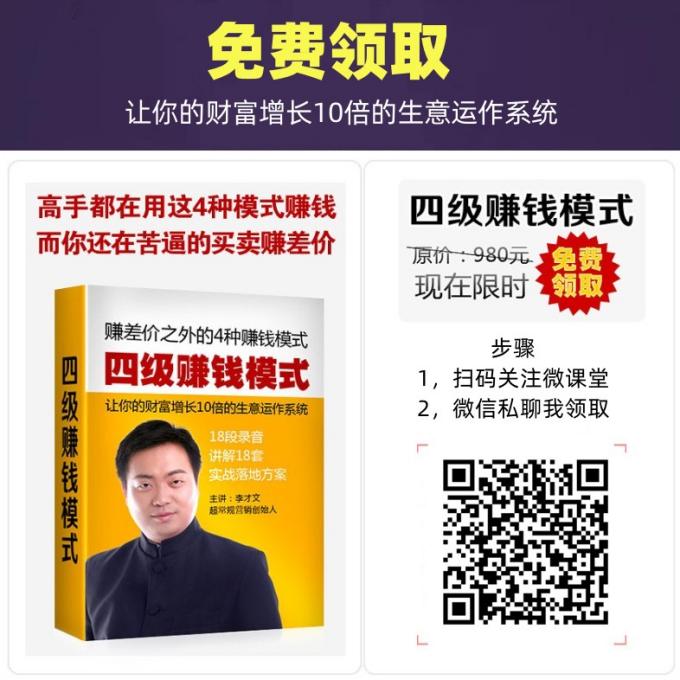