碳酸钠和二氧化碳
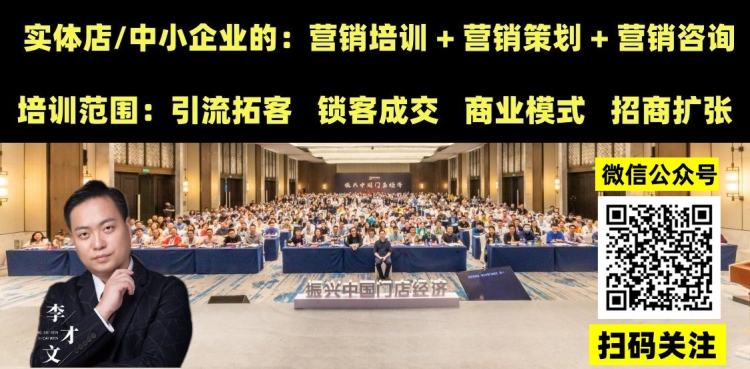
近年来,随着煤炭资源的紧张和质量的变差,加上负荷的增加,湿法脱硫过程中副反应的问题愈发严重,这导致了生产过程中的消耗增加和设备的腐蚀。下面我们将详细分析脱硫生产过程中的副反应及其原因和影响,并提出相应的解决办法。
1. 副反应概述
在脱硫生产过程中,除了主反应外,还会伴随有碳酸氢钠、硫代硫酸钠、硫酸钠、硫氰酸钠等盐类的副反应生成。这些副反应的发生,不仅影响了脱硫效率,还导致了设备的腐蚀和工艺的复杂化。
1.1 副反应的原因
(1)原料气中的二氧化碳与碳酸钠作用,发生碳酸化反应,生成碳酸氢钠。当其他因素不变时,提高气相二氧化碳分压或降低液相二氧化碳的平衡分压,会增大吸收速率。
(2)硫氢根与氧接触时,会发生硫代硫酸盐的生成反应。
(3)若液中溶解氧量过高或溶液与空气接触时间过长,将会有较多的硫酸盐生成。
(4)原料气中的氰化氢几乎全部被碱液吸收,生成,并进一步生成硫。
(5)溶液中的悬浮硫也会发生副反应。
(6)在再生氧化过程中,若液中催化剂的量低,则因双氧水过剩而发生副反应。
(7)在高温熔硫时,硫与碱及其它物质反应较迅速,有大量副盐生成。
1.2 副反应的影响与危害
(1)副反应会影响脱硫效率,降低溶液的pH值,对析硫不利。
(2)副反应严重会导致碱耗剧增,影响吸收与再生,造成生产被动和生产成本增加。
(3)副盐的增长还会加剧溶液对设备的腐蚀,影响传质和传热,不利于吸收和再生。
(4)副盐的高含量还会降低硫的回收率。
1.3 解决办法
针对上述副反应,可以采取以下措施:
(1)通过调整工艺条件,如使用再生技术提高再生效率,降低溶液中CO2的物理溶解量,从而降低副反应的发生。
(2)适当加强再生过程管理,保证富液在反应槽内停留一定时间,减少进入再生系统的硫氢根的量。
(3)注意溶液中各组分含量适当,操作条件适宜,使析出硫黄颗粒大,并加强过滤。
(4)控制溶液温度在适宜范围内,既保证了吸收和再生反应正常进行又降低了副反应速度。
2. 设备的腐蚀及其原因
设备的腐蚀主要是由于化学腐蚀、电化学腐蚀、氢去极化腐蚀等多种因素共同作用的结果。特别是在积硫处、气液相界面部位、器部分等地方,腐蚀较为严重。
2.3 减轻腐蚀及方法
为减轻设备的腐蚀,可以采取以下措施:
(1)通过控制溶液的组分含量和pH值,减少副反应的发生,从而减轻腐蚀。
(2)保证设备管道内的溶液保持小流动或定期排放,防止硫沉积。
(3)对易发生严重腐蚀的部位进行打砂环氧处理。
(4)使用脱盐水来配制溶液并作为补充水,以减少对设备的腐蚀。
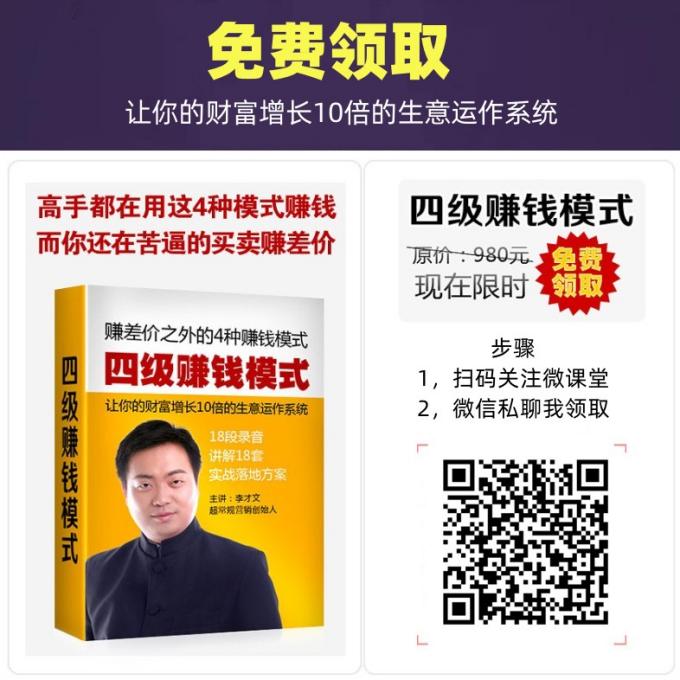