液体胶怎么用效果最好?试试这几招,让你的手工作品更完美!
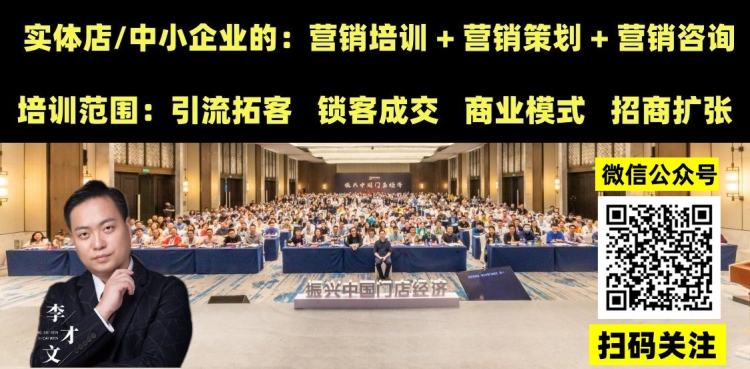
一、技术革新:从高温高压走向分子级精准脱硫
传统的再生胶脱硫工艺依赖高温高压环境,不仅消耗大量能源,还产生废气。环保型液态脱硫工艺通过液态介质实现了分子级的精准破键。在螺旋脱硫装置中,胶粉与新型软化剂、活化剂在常压下混合,借助电磁加热和机械剪切协同作用,使硫化键在温和的120-150℃条件下断裂。据某企业实测数据,这一新工艺的能耗相较于传统工艺降低了70%,并且实现了废水、废气的零排放。这种创新的技术的关键在于液态介质起到“桥梁”作用:新型活化剂分子嵌入橡胶网络,使得微波或电磁能直接作用于硫键,大大提高了能量利用率。某实验室模拟数据显示,液态脱硫的能量利用率高达85%,远超动态脱硫的55%。这一技术革新显著提升了脱硫效率和质量。
二、成本重构:规模化生产的经济性优势
虽然液态脱硫生产线的初期投资约为500-800万元,略高于传统动态脱硫的200-300万元,但其长期运行成本优势显著。采用液态脱硫后,单位能耗从1.2kWh/kg降至0.4kWh/kg,综合成本下降35%。更重要的是,液态脱硫无需复杂的废气处理设备,仅需闭式循环系统即可满足环保要求,从而节省了额外的设备成本。液态脱硫的连续化生产特性提升了产能,处理效率提升40%。某企业案例显示,其月处理量跃升至700吨,单位处理成本也大幅下降。值得注意的是,液态脱硫对胶粉细度的要求较低,预处理成本也相应降低。
三、环保:零污染背后的三重防护体系
液态脱硫工艺在环保方面表现出色。其密闭反应腔体将VOCs浓度控制在50mg/m³以下,仅为动态脱硫的1/3。液态脱硫的废水产生量及污染物浓度均较低,处理难度大幅下降。更重要的是,液态脱硫实现了资源的闭环利用:脱硫剂可循环使用50次以上,再生胶中硫磺的回收率高达92%,远高于传统工艺。这一创新技术不仅降低了企业的废气处理成本,也提高了资源利用效率。
四、性能跃升:赢得中高端市场的入场券
液态脱硫胶料的分子结构保留了更多长链聚合物,使其性能得到显著提升。检测数据显示,液态脱硫胶料的扯断伸长率高达550%-650%,较动态脱硫提升60%,拉伸强度也相应提高。某轮胎厂试用结果显示,使用液态再生胶的轮胎胎侧疲劳寿命延长35%,良品率也大幅提升。这些性能优势使得液态脱硫胶料在汽车密封件、高铁减震垫等高端领域的应用比例大幅提升。液态脱硫胶料的可塑性指数满足子午线轮胎胎体胶的工艺要求,进一步拓宽了其应用领域。
五、应用趋势:红利与市场机遇共振
欧美市场对液态脱硫技术的普及率已超40%,且德国某企业通过该技术实现了高轮胎翻新率,产品进入高端供应链。国内市场虽然仍以动态脱硫为主,但倒逼效应显著。随着国产化设备的突破和技术的普及,液态脱硫技术在国内的应用趋势日益明显。某上市企业投资建设的液态脱硫产业园和推出的常压连续脱硫机组等实例也证明了这一点。
实务策略建议:
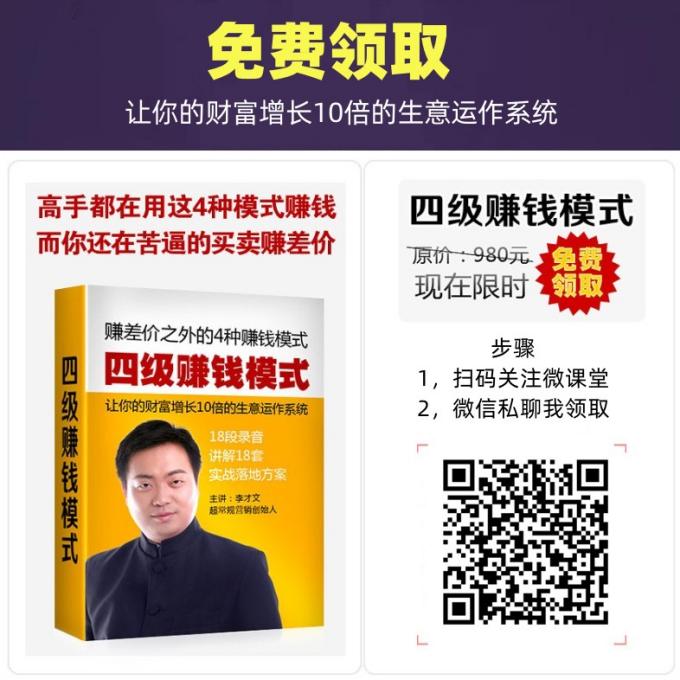