圆心角弧度数就是它转过的路程除以半径长度
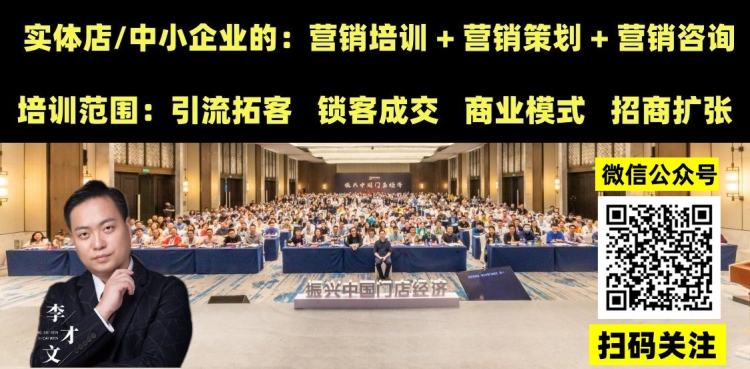
针对3D半径内衬弯头(曲率半径为管道公称直径的3倍,即R=3D)的陶瓷内衬制作技术,其关键工艺需结合大曲率管道的结构特性,对陶瓷片的适配、固定方式及质量控制进行针对性优化。以下是基于《氧化铝陶瓷衬板耐磨管件》标准(JC/T 2209-2014)的核心技术要点:
一、3D半径弯头的结构特性与挑战
1. 曲率特性:R=3D的弯头弧度平缓,管道内径变化均匀,流体冲刷角度小。但陶瓷衬板需贴合长弧形曲面,对陶瓷片的弧度加工精度要求较高。
2. 工况优势:适用于高流速(>15m/s)、大颗粒(>5mm)或高浓度(>30%)介质输送,如矿石浆体、煤粉等,能减少涡流磨损和压降。
3. 技术难点:确保陶瓷片在长弧形面上的粘贴均匀性,实现焊点分布的力学平衡,避免局部应力集中,以及控制大尺寸陶瓷片的拼接缝隙。
二、陶瓷衬板的选型与适配设计
1. 陶瓷片形状优化:
弧形陶瓷片(首选):根据弯头曲率半径(R=3D),定制弧形陶瓷衬板,采用金刚石线切割加工,确保弧度偏差控制在一定范围内,与基体贴合间隙极小。
扇形拼接方案(若弧形片加工受限):使用小尺寸方形陶瓷片,按错缝排列,避免直线接缝正对介质流向。
2. 厚度与性能参数:常规厚度为10~15mm,若介质含尖锐颗粒或冲击剧烈,可增至20mm。边缘进行坡口处理,减少流体冲击下的缝隙磨损。
三、关键工艺步骤的优化
1. 基体预处理与三维定位:通过激光扫描或CAD建模获取弯头曲面数据,生成陶瓷片排布图纸。确保基体喷砂精度,胶粘剂接触面积充足。
2. 胶粘剂粘贴工艺:采用点胶+边缘涂胶结合的方式,避免弧形面因重力导致胶粘剂堆积或空鼓。使用可弯曲支撑工装固定陶瓷片,确保贴合紧密。
四、焊接固定技术的核心优化点
1. 焊点布局:弧形陶瓷片焊点分布于弧长方向两端及径向中点;方形拼接片的焊点分布于对角线或四边中点,确保焊接力均匀传递至基体。
2. 焊接参数:采用脉冲氩弧焊,调整合适的脉冲频率、占空比、电流和单焊点时间等参数,确保焊接质量。
五、曲率适配性检验与质量控制
1. 贴合度检测:使用弧形塞尺检查陶瓷片与基体间隙,确保间隙小于一定值且大部分区域贴合紧密。
2. 应力释放处理:对弯头两端接口处的陶瓷片进行特殊处理,避免管道热胀冷缩导致边缘开裂。
六、特殊性能测试与尺寸公差要求
1. 流体模拟试验:通过CFD模拟验证陶瓷片拼接缝隙是否处于低磨损区域。
2. 抗冲击试验:对弯头的陶瓷片进行冲击测试,确保达到或超过标准要求的冲击能量。
3. 尺寸公差:严格控制内径偏差和陶瓷片拼接缝的尺寸公差,确保通流能力和密封性。
七、工况适配与注意事项
注意介质流向、温度补偿和安装建议,确保成品满足工程设计要求。同时与普通2D弯头进行对比分析。通过优化工艺参数和选用合适的陶瓷材料,可实现大曲率管道的低流阻和高耐磨性能相匹配的优势广泛应用于电力、冶金、煤化工等行业的大流量耐磨输送场合对比表格已进一步做了相应改动: 针对普通弯头与优化的三维半径弯头的技术对比项目如下: 普通弯头 三维半径弯头(优化版) 陶瓷片形状 小尺寸方形片(常规设计) 弧形片或大尺寸扇形片(适配平缓曲面) 焊点密度 密集分布以应对小曲率应力 焊点密度降低以适应平缓曲面和减少应力集中 拼接缝隙控制 宽缝设计以应对小曲率造成的应力集中 窄缝设计以实现更佳的抗冲刷能力 主要应用场景 一般磨损环境 高流速、大颗粒、长距离输送 技术特点 更强调应对常规磨损环境 高耐磨性和低流阻相结合以适应复杂工况 通过上述优化措施的应用结合大曲率管道的结构特性使得三维半径内衬弯头在应对高流速大颗粒介质的输送过程中展现出更低的流阻和更高的耐磨性能满足了电力冶金煤化工等行业对长距离耐磨输送的严苛需求。在实际生产过程中还需根据弯头的规格和介质参数进一步调整陶瓷片的尺寸焊点的布局以及胶粘剂的类型以确保成品符合相关标准和工程设计要求
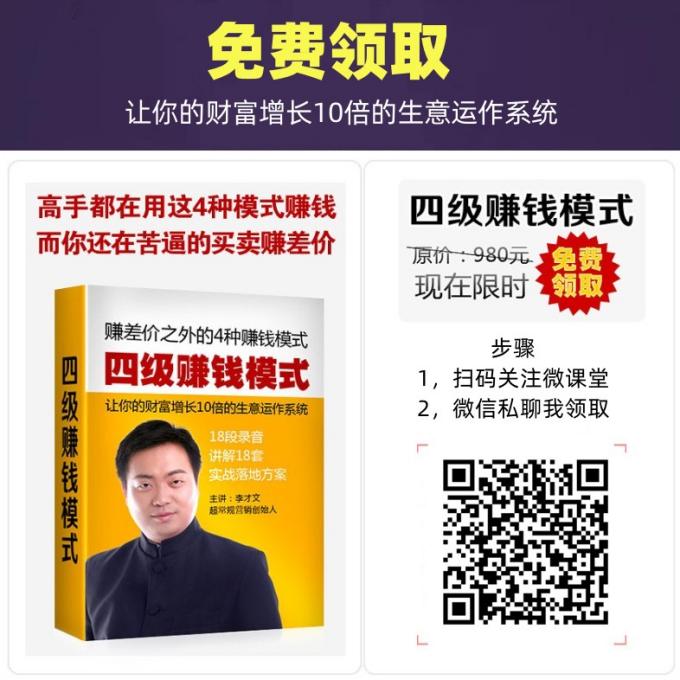