cpk是什么_cpk数据分析怎么做
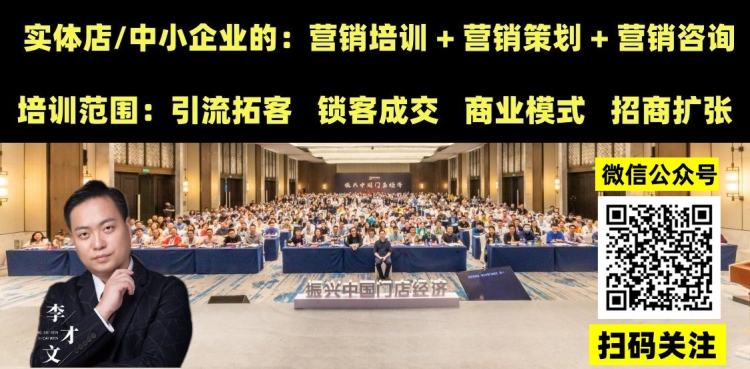
PPK与CPK概述
PPK(Process Performance Index)着眼于过程在一段时间内的表现,不考虑过程是否偏移,其容差范围除以过程性能。这一指标主要适用于小批生产(试产)的过程性能评价,要求PPK值大于1.67。它关注所有数据之间的变差,包括普通因素和特殊因素产生的变差。
CPK(Complex Process Capability index)则考虑过程存在偏差时,样本数据的过程性能。它表示过程本身的能力,是一种理想状态下的指数。CPK的计算要求过程稳定、有足够的历史数据或初始数据,并且常用于大批量生产后的生产能力评价。该指数主要区分普通原因变异和特殊原因变异,只考虑子组变差,剔除组内变差。
PPK与CPK的区别与应用
1. 应用场景:
PPK常用于初期数据匮乏的案例,尤其在客户同意后可采用以评估过程性能。
CPK则用于周期性的过程评价及稳定过程的持续监控。
2. 取样方式:
PPK的取样不需要间隔一小时,可连续取100个数据。因其不要求检查过程是否稳定,故其计算过程中已考虑了变差的两种因素。
CPK的取样则需遵循一定的时间间隔,如每天取一组数据(通常5个),且要求过程稳定及有充足的历史和初始数据。
3. 计算与解读:
PPK和CPK的计算公式中,δ的计算方法有所不同——PPK采用标准差公式计算,而CPK使用经验公式。这导致了两者在变差计算上的差异。
若CPK值与PPK值相差不大,表明过程受特殊因素的影响较小;相反,则说明特殊因素对过程影响显著。若CPK比PPK小且有控制图上的异常点,则可能表明过程未受控或计算结论有误。
4. 与质量及PPM的关系:
当供应商的CPK分析得出1.33的结论时,这并不等同于特定的PPM值。对于非临界数值的CPK值,需进一步分析以预测PPM及相关的报废率和质量成本损失。
总结:
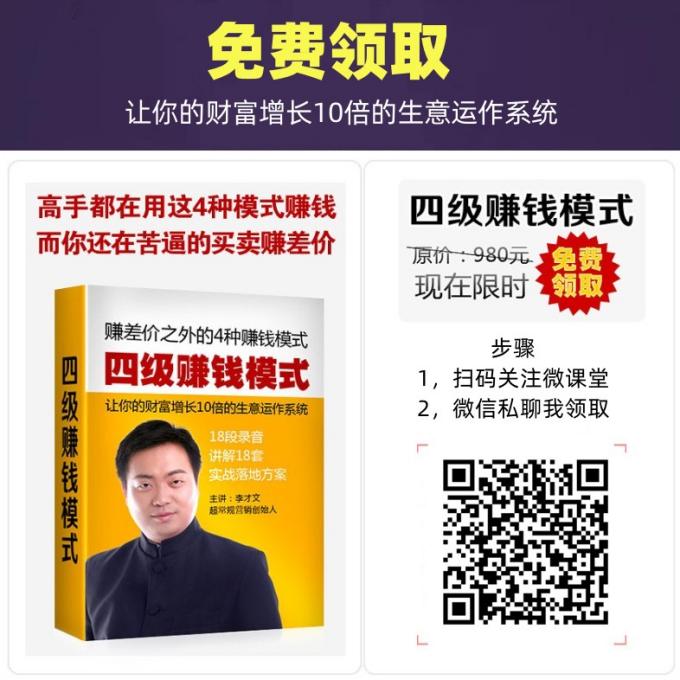